Inside R&D at VATA
Today, we’re thrilled to give you an exclusive look into the Research and Development (R&D) process here at VATA, led by our very own—and very talented—Product Design Manager, Kyle Pierce!
But first, a quick intro to Kyle:
Prior to joining the VATA team in 2021, Kyle honed his engineering skills working in the biopharmaceutical industry, specializing in labware design for research. Now, as VATA’s Product Design Manager, Kyle leads our product development team. Their goal? To create cutting-edge products that advance the standard of quality and realism in medical simulation.
A lifelong learner, Kyle is fascinated by the procedures, devices, and innovations of the medical world. He relishes opportunities to learn new things and create new products to help clinicians ultimately enhance patient care and safety.
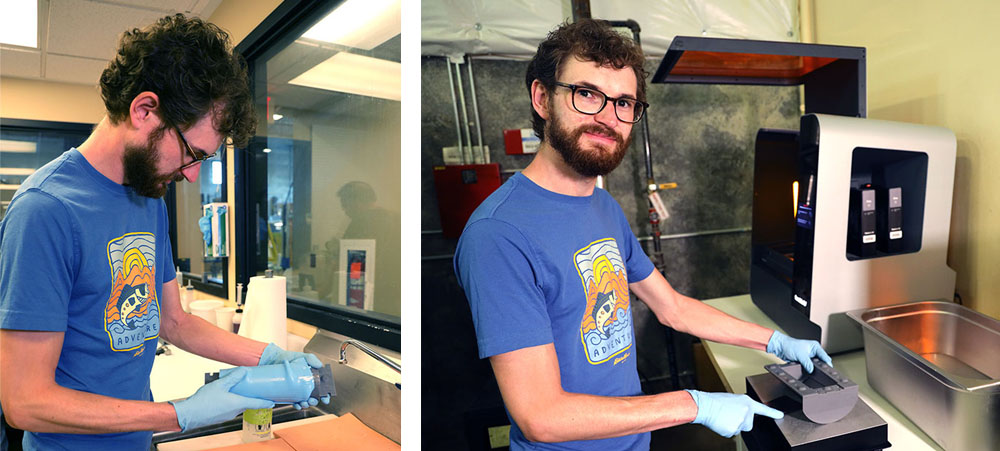
Thank you, Kyle, for taking the time to talk R&D. Let’s dive in:
What’s your typical process for designing new products?
The first step is to gain an understanding of the procedure we’re simulating. We talk to customers, industry partners, and field experts to develop a list of necessary model features. Next, we generate initial design concepts. The goal is to be creative and find the most robust and practical way to provide all of the features we decided on in the first stage. We build proof-of-concept mockups and evaluate internally. Once we select the best option, we build our first prototype. This prototype will include all of the necessary features and will be aesthetically similar to the final product. Customer and industry feedback on the prototype guides modifications. Based on the complexity of the project and nature of the feedback, the feedback-redesign process may even repeat several times. Once a design is finalized, tooling is made, components are sourced, and production begins!
How do you decide which features to focus on during R&D?
This may sound cliché, but the most important features in a design are the ones that are important to our customers. We want to ensure our products address real-world challenges effectively, and customer and industry partner input influences everything from product materials and size to pricing and aesthetics.
When we speak to customers and industry partners, they often share what they like and dislike about existing products on the market. And when they review our prototypes, they offer invaluable, honest feedback on components of the design that hit the mark and features that could use improvement. Customer needs and feedback drive our design, decision-making, and ultimately, shape our innovations.
How does customer and clinician feedback factor into new product development?
Customer and clinical feedback is one of the most important factors in creating a successful design. We use industry feedback to help us decide which new product ideas to pursue, which aspects of a medical procedure to incorporate into a new simulator, and to evaluate the effectiveness of new design features. All of these things are critical to delivering products that customers enjoy working with.
How has VATA’s R&D process evolved over the years?
The improvement of 3D printing over the last decade has had a significant impact on our product development process. Prior to this, our products were mostly hand-designed by skilled sculptors. Parts would be sculpted to create shape, skin textures, wounds, and other product features. While these same sculptors still work on new products, 3D CAD, scanning, and printing now play a big part in the design process.
We now use a machine to digitally scan human body parts into our 3D modeling software. This allows us to create new designs much faster because we don’t need to physically make each design iteration. For making proof of concepts, prototypes, and even some production parts, 3D printing allows us to build the complex features of our simulators quickly and cost-effectively. With these three pieces of technology, our development process looks a lot different than it did just ten years ago.